Figure 1: 3D Printing illustrating Local Composition Control (LCC)
One of the great potential benefits offered by
Solid Freeform
Fabrication (
SFF) technology is the ability to create
parts that have composition variation within them. Such
Local
Composition Control (
LCC) has the potential to create new
classes of components. Material composition can be tailored within a
component to achieve local control of properties (e.g., index of
refraction, electrical conductivity, formability, magnetic properties,
corrosion resistance, hardness vs. toughness, etc.). By such local
control, monolithic components can be created which integrate the
function of multiple discrete components, saving part count, space and
weight and enabling concepts that would be otherwise impractical.
Controlling the spatial distribution of properties via composition
will allow for control of the state of the entire component (e.g., the
state of residual stress in a component). Integrated sensors and
actuators can be envisioned which are enabled by LCC (e.g., bimetallic
structures, in-situ thermocouples, etc.). Devices which have as their
function the control of chemical reactions are possible. The utility
of
Mesoscopic parts made by SFF will depend strongly on the
ability to locally control composition.
Realizing the
potential utility of LCC in SFF is a many-faceted challenge requiring
developments in the: (1) Information technology and design tools
required to support the design of parts with LCC; (2) Extension and
characterization of the range of materials which can be deposited with
local control (SFF technology specific); (3) Design of materials
systems with locally varying composition which can be successfully
treated in operations subsequent to the SFF process itself (e.g.,
densified in a furnace firing operation); (4) Exploration of specific
applications of LCC.
The work reported here focuses
primarily on the issue of Information Technology and Design Tools -
(1) above. The absence of knowledge, methods and tools in this area
presents an absolute bar to the exploration of materials systems and
applications. Developments in these areas will allow a wider
community to contribute to materials and applications.
Information Technology and Design Tools may be divided into
two categories: (1) tools which are generic, and (2) tools which are
specific to a given SFF process. Generic electronic representations
must be developed to allow for electronic specification within a
component. There must be a suite of tools which allows a designer to
communicate with this representation using high level features that
are sensible to a designer. The designer must be able to visualize
and interrogate the evolving model. The model must not allow the
designer to request that which cannot be made. Process specific tools
include methods to render desired continuous composition profiles in
the discretized form required by a specific process and the generation
of machine specific fabrication instructions.
Wherever
possible, the work conducted under this project will be generic and
applicable to a broad range of SFF technologies. However, in the
cases where the outcome is process specific,
Three-Dimensional
Printing (
3D Printing) will be used as the prototypical
SFF technology. Among the SFF processes, 3D Printing is particularly
well suited to the fabrication of parts with LCC. 3D Printing creates
parts in layers by spreading powder, and then ink-jet printing
materials into the powderbed. In
some cases, these materials are temporary or fugitive
glues, but
in many cases, these materials remain in the final component.
Examples of the latter include; ceramic particles in colloidal or
slurry form, metallic particles in slurry form, dissolved salts which
are reduced to metal in the powderbed, polymers in colloidal or
dissolved form, and drugs in colloidal or dissolved form. 3D Printing
has been extended to the fabrication of LCC components by printing
different materials in different locations, each through its own
ink-jet nozzle(s). Figure 1 illustrates this
conceptually with two different colors, each representing the printing
of a different material into the powder bed with local control of
position. 3D Printing is thus capable of fully three dimensional
control of composition.
Figure 2: Information Pathway
|
The LCC information pathway with 3D
Printing begins with a designer interacting with a standard CAD system
to define the shape of the object, see Figure 2.
The solid model thus created is then
exported from the CAD system as a standard exchange format such as
STEP or IGES. In the course of our prior
work, we implemented an LCC modeler based on tetrahedral mesh
data structure. This finite-element based LCC modeler can be thought
of as a special instance of our generalized cellular decomposition
approach to LCC modeling. It was
chosen as a convenient method to demonstrate the information pathway
and to explore the issues associated with LCC. Once the geometry of
the model is fully defined, it is loaded into a finite-element mesh
generator via a neutral format, and meshed into a set of tetrahedra.
This process is referred to as pre-processing in Figure
2. The composition of a part is established
by specifying the composition values at the vertices of each
tetrahedron and interpolating between them. As an exemplar of a
design tool, we developed a method to specify a composition profile
normal to the surface and apply this profile to an entire object.
Post-processing (see also Figure 2) then converts the designed LCC model
into instructions for the 3D Printing machine.
Post-processing takes place on a layer-by-layer basis
along two parallel paths: (1) the accurate definition of the surface
(Geometry Slice); and (2) rendering the composition of the body
(Material Slice). The continuous-tone material composition is
rendered into printable discrete information using haltoning (or
dithering) algorithms. The boundary and composition information is
recombined to produce the drop-by-drop instructions that are loaded
onto the 3D Printing machine. Special attention is given to
reconciling conflicts which occur at the boundary where the designer's
intent in both composition and surface finish must be recognized.
The complete information and 3D Printing pathway have been tested and
demonstrated with a part of representative complexity
as shown in Figure 3.
The part is an injection molding tool and the
design challenge is to place hard phases in a designed composition
profile near the surface. In this demonstration, two colors of ink
were printed (magenta and cyan) with the condition that the sum of
the materials was everywhere constant. The bottom image in Figure
3 shows a photograph of a layer of the actual printed part.
This can be compared with the material and
geometry information above it, which become merged to produce the
instructions which led to the printed part.
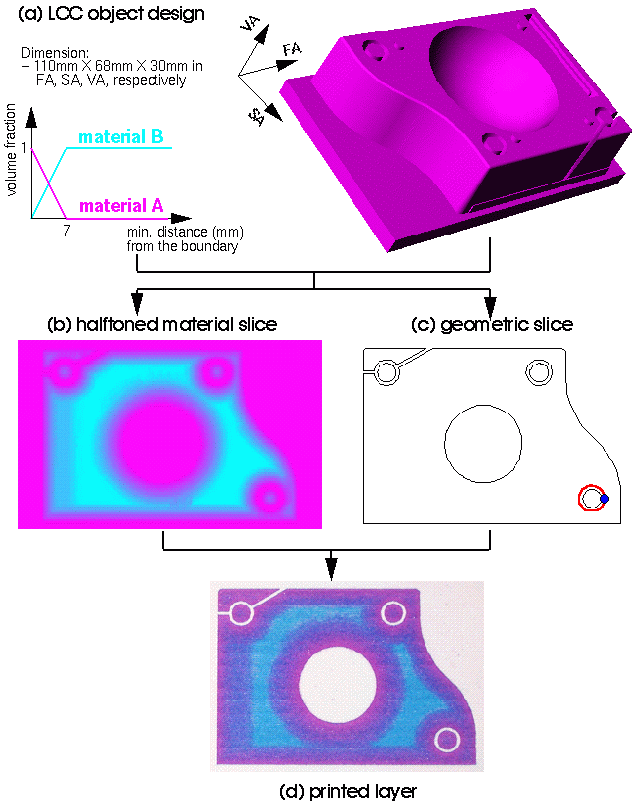
Figure 3: Demonstration of Information Pathway